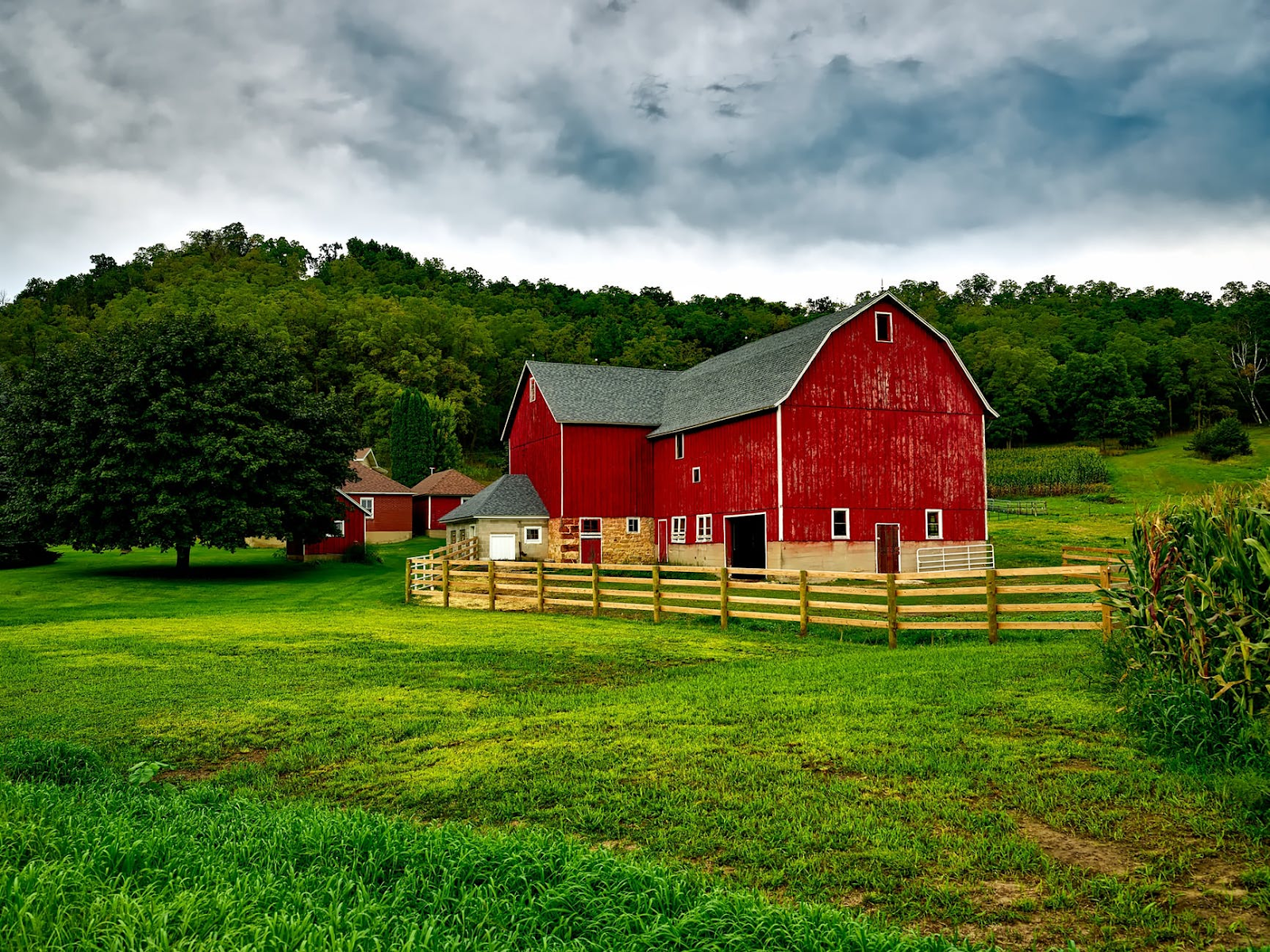
For milk to be safe for human consumption, it has to go through a dairy processing plant. These processing plants are large facilities, with various sections and moving parts required to process milk from start-to-finish.
Processing plants are required to meet strict requirements, which are set by both the FDA and USDA. The requirements largely focus on maintaining a safe, sanitary, well-functioning facility. There are many factors that go into creating a safe and sanitary facility, each important in their own right. However, these are three critical things every dairy processing plant should make sure they have, above all else.
1. Invest in the Best Plant Machinery
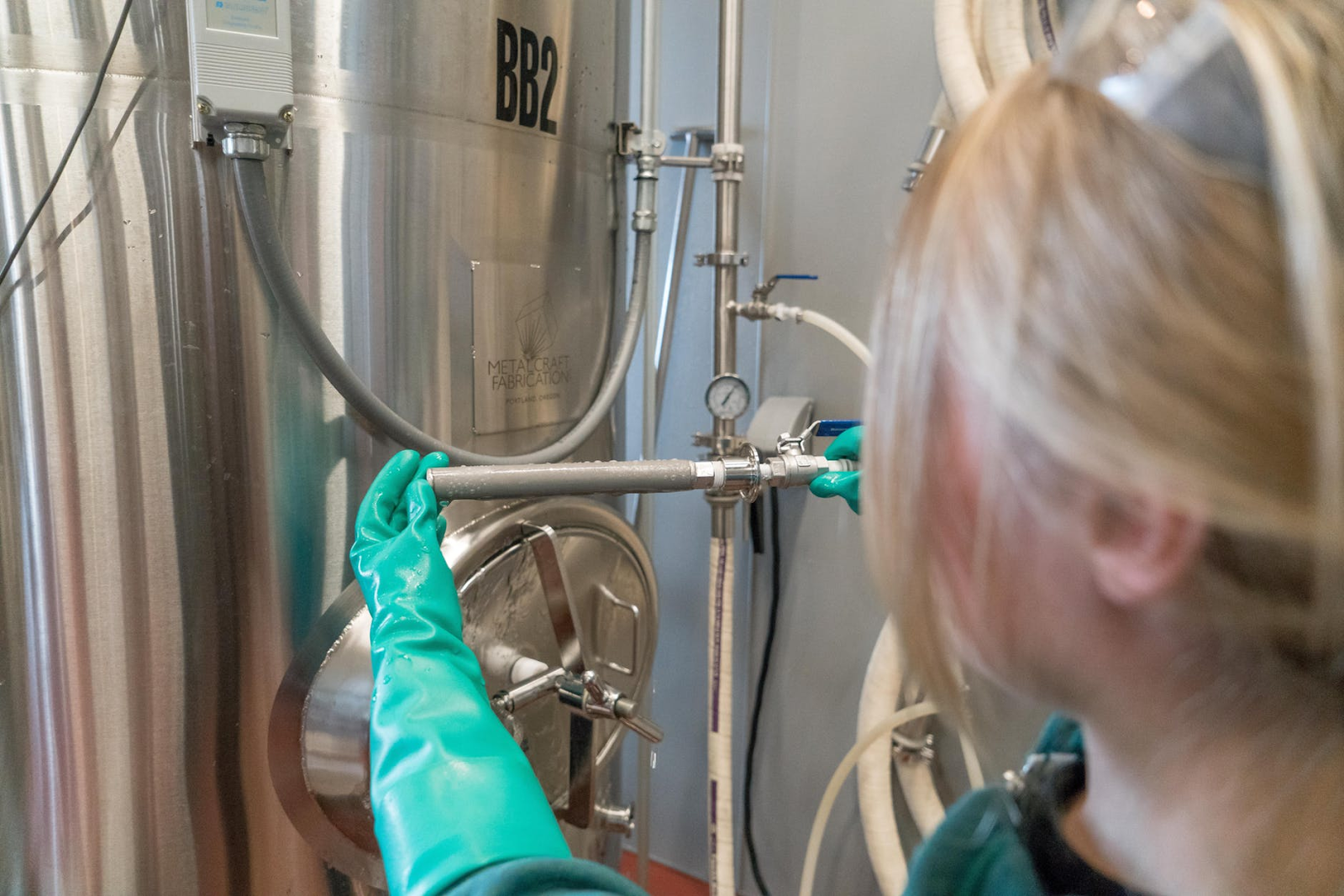
First and foremost, a dairy plant needs all the right dairy processing plant equipment to even function. There isn't just one or two pieces of equipment a facility needs, but a whole plethora. From the equipment to test the freshly transported milk for antibiotics to the bottling equipment, every stage of the processing plant requires some sort of special equipment.
First, there is the lab equipment that workers use to test samples of newly arrived batches of raw milk. Anything within the lab needs to be sterile to ensure the tests for milk fat, protein, bulk milk cell count, and bacteria count are not contaminated. Milk that passes the testing process will move to stainless steel holding tanks or silos as it is prepared for processing.
Pasteurized milk will then go through a homogenization machine to help evenly distribute the fat in the milk. Once that has been done, a centrifuge will separate the milk and cream, and then recombine the two to create the desired fat content level of the milk.
Finally, milk may go through a micro-filtration machine, which helps increase the storage life through the use of ultra-high temperature treatment. Once all the processing is complete, the finished product will move to bottling and packaging, then cold storage, before it is transported to stores.
All of this equipment should feature food-grade stainless steel construction that is bacteria-resistant and easy to sanitize. In addition, equipment should be serviced every few months to ensure it is always in top working condition, with no chance of it failing or causing any sort of issue that can lead to plant failure, injury, or possible product contamination.
2. Have Reliable, Well-Trained Employees
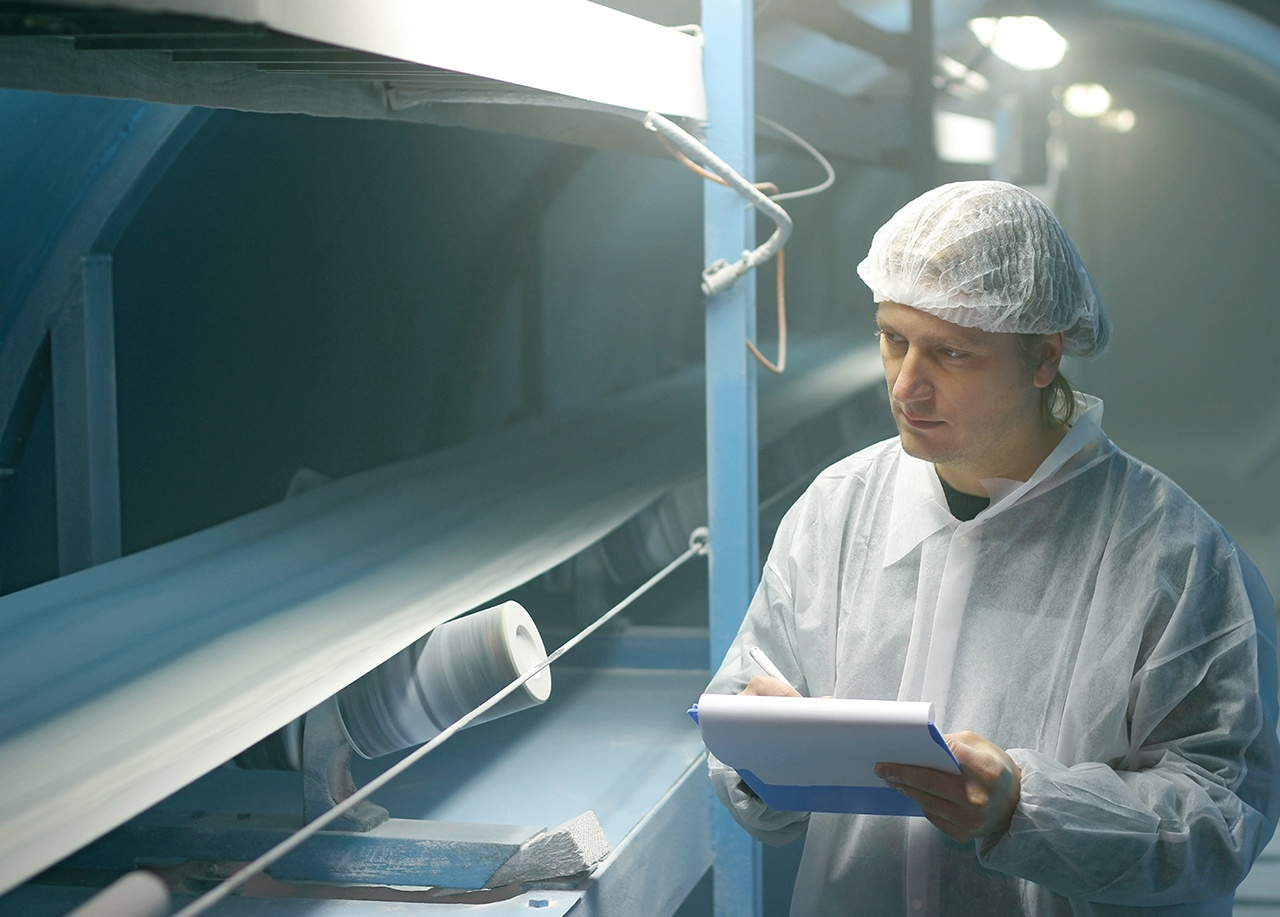
While having the right dairy processing plant equipment is one critical thing every dairy plant requires, it is not the only thing. You can't have a dairy processing plant without a team behind you, after all.
It is your team of employees that handles everything that happens in the dairy plant. From the testing and accepting of fresh milk to controlling the machines, even then, the most automated of facilities needs humans to keep things running smoothly. They are also the ones responsible for helping to keep the whole dairy processing plant clean and sanitary.
However, just having employees to run your facility isn't enough. You want to ensure that each and every employee you hire is highly trained and incredibly reliable. Employees should receive training not only in the area they were hired but also cross-trained in order to help in a different part of the facility.
In addition, all employees should know how to handle various scenarios, such as machine failure, safety issues that could arise, or any other issue that could present itself.
Beyond that, you want to stay on top of employees' training by providing refresher courses so that employees never forget how to do other jobs or handle emergencies. It can truly help to increase the plant's efficiency and help prevent employee errors from occurring.
3. Have the Right Floor Drainage System
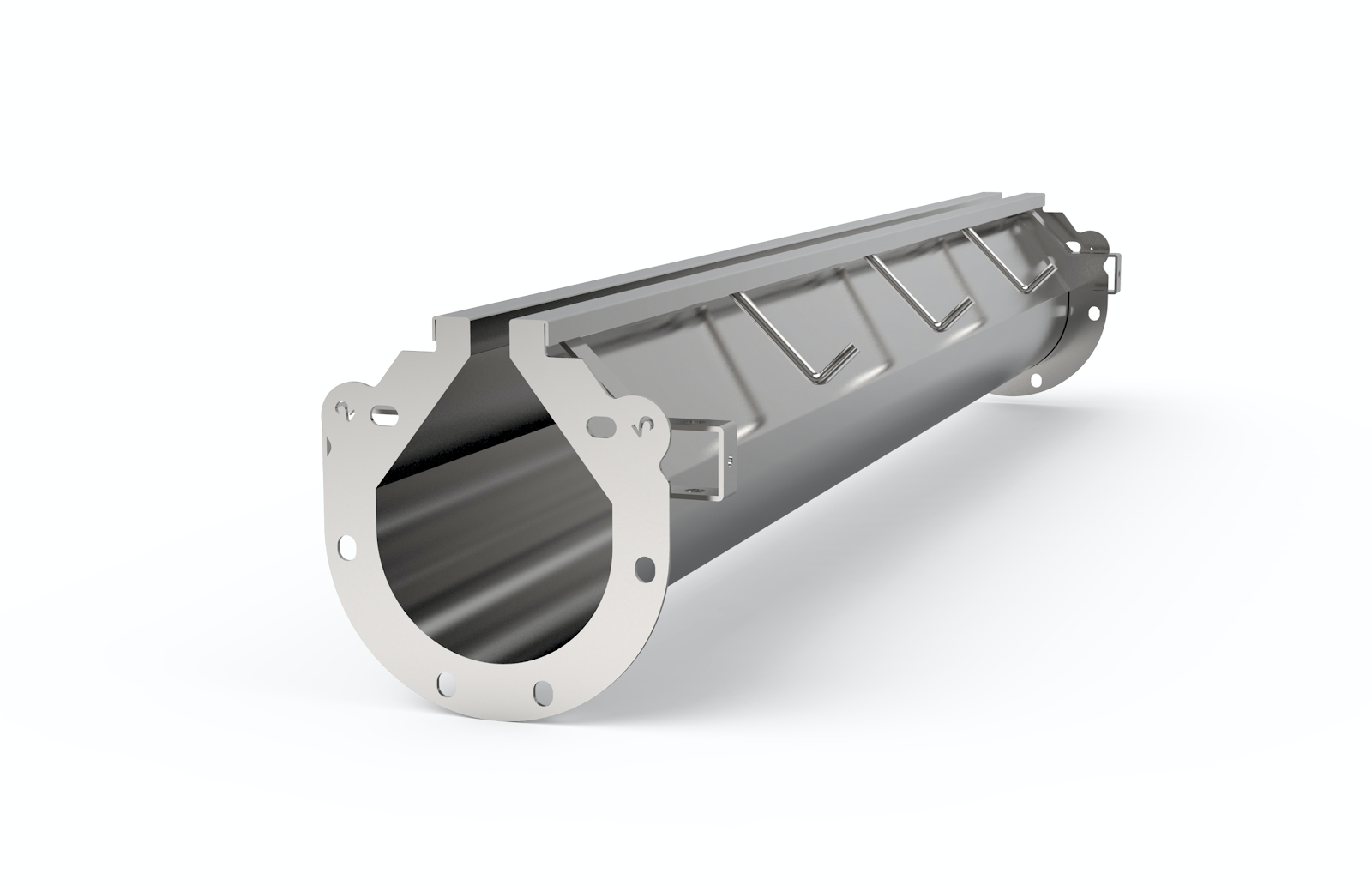
Though often overlooked, tying a whole dairy processing plant together is the floor drainage system. Floor drainage is something every facility, especially those dealing with food and beverages, needs. Drainage systems are what help to create and maintain, safe and sanitary facilities that are free from bacteria and other contamination. They will also ensure that the floors of the facility remain dry and slip-free.
By far, the ideal floor drainage system is one from Slot Drain. They have created an easy-to-install trench drain system that comes both pre-sloped and pre-assembled. Unlike other trench drain systems on the market, however, the Slot Drain system has the added benefit of being very slim, modern, and free of cumbersome grate coverings.
Slot Drain comes with a food-grade, stainless steel drain channel that is bacteria- resistant, corrosion-resistant, and resistant to extreme temperatures. All of these make it a great piece of dairy processing plant equipment to have within a facility.
Adding to the benefits of a Slot Drain is how easy it is to clean and maintain. There are options to have automatic Clean-in-Place and Flush Flo systems included with the unit, drastically cutting down on the work that employees have to do. Without a cumbersome grate covering, employees will also have an easier time inspecting the drain channel to ensure it is thoroughly cleaned of any debris, and a brush and paddle will catch whatever is left.
Three Things That Make a Big Difference
A dairy processing plant is a place that requires careful planning and extreme attention to detail. You want to ensure your facility is set up for success. Otherwise, it can lead to a multitude of issues–including potentially serious ones. While there are countless important things you want to have for your facility, the three listed above take priority.
Without the right dairy processing plant equipment to fill the facility, well-trained employees to help run it, and the right drainage system to keep everything sanitary, a dairy processing plant will not be successful. Therefore, it is absolutely crucial to keep all of these things in mind when setting up a new dairy facility, and take the time to set it all up the right way.